Alternative Solutions
As part of our mission to be thorough in our workings, we analysed a multitude of other alternative solutions to the problem posed by the Imperial Chemical Company. This is to ensure our client has choice and control over what they wish to implement to their plants. We understand different companies will have different requirements and this is our way of ensuring we fulfil as many of those requirements as possible.
​
Below we have included 2 of our other solutions to their problem. Despite not being the most optimal solution to their problem they still fulfil their purpose of decreasing the running cost of the plant, albeit not to the extent of our proposed solution. Please note, our alternative solutions revolve around fixing the problem concerning stream 3 and thus no detail about streams 1 and 2 will be given as we believe these are already at a optimal state from our proposed solution.
Solution 2
For our second solution, we wanted to focus primarily on the system of heat exchangers around stream 3 (figure 1.6) in the plant. This is because we felt that our solution for connecting streams 1 and 2 we're already optimal and wanted to experiment around stream 3 as this is the most costly stream and so the most important.
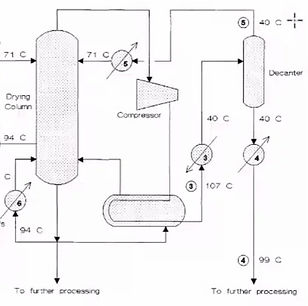
Figure 1.6

Figure 1.7

Figure 1.8
We decided to implement this system of heat exchangers (figure 1.8) as the C value associated with stream 4 was extremely low (figure 1.7) compared to the other streams. This meant very little energy would be needed to heat stream 4 to the desired temperature. This results in the cost of heating stream 4 to be relatively small. In addition, there would be no cost associated with purchasing a heater as we can use the original heater.
​
After stream 3 passes through streams 5 and 6 it still requires further cooling to reach the desired temperature. Therefore, an additional cooler is needed. Fortunately we can reuse the one already in place and so we just had to calculate the cost of running this cooler.
If we sum up the cost of installation and running of the heaters and cooler. The total cost comes to £322,000 over a period of five years. If we compare this to the original cost of £1,250,000 over a period of 5 years, we can see this is also drastically lower. However, as we explained above, this is not the optimal solution and so we decided to present this as an alternative solution. The benefit of this solution is that two of the heater/coolers can be reused. This may be appealing from an environmental perspective.
Solution 3
Similarily, our third solution focused on finding a correlation between the temperature difference and the cost of heating. Focusing on the streams around stream 3, we wanted to investigate if the stream with the lowest temperature difference can be heated normally using a heater. In this case that was stream 5 as there is only a temperature difference of 31°C. This system of heat exchangers is similar to solution 2 (figure 1.9).

Figure 1.9
As we can see from the tables the biggest issue with this solution is the massive cost of steam and water for the heating/cooling of streams 5 and 6. Clearly there is no correlation between the temperature difference and the cost of heating. The total cost of this solution over a period of 5 years is approximately £821,707.78, which is still much less than the original cost over the same period however it is much higher than our other solutions.